Ordering and inspecting product sample from Alibaba supplier for Amazon private label
One of the necessary and important steps in the process of manufacturing our own private label product on Amazon or purchasing product from wholesaler/supplier/factory on Alibaba, or producing our own products to sell on different channels, is to order a product sample from the supplier/factory that we are considering working with and examine it in depth.
Why is it important to order a sample from the supplier before starting production?
Ordering samples from the factory/supplier helps us to understand the factory’s quality of production, how our product can look like, examine the product characteristics and its resistance to different conditions, to test what is working well and what we would like to improve or repair before we start mass production.
Inspecting a product sample will help you to make sure you and the supplier are on the same page, and to prevent disappointment, damages, financial loss and valuable time, further down the road.
It’s also a great way to test your supplier’s service and capabilities, and how he/she responds when you ask for making any changes or improvements to their sample.
How to order a sample from your Alibaba supplier?
If you do not make a sample from scratch, ask for several samples of the same model, 4-5, and not one. This is because most of the samples you will receive from the supplier are samples from a stock that is already exist.
Ordering several samples can help you examine the consistency of the supplier’s production process and quality (Are there any differences in the production of the product?)
Sometimes it is better to consider ordering several different models so that you can choose the one that is most suitable for your needs.
Keep in mind that the cost of the sample will usually be higher than the production cost (per unit) since it is one unit and not mass production, and both parties are still considering the possibility of doing business with each other. However, this financial investment worth the learning and understanding you will receive about the quality of the factory that you want to work with, the product quality, and how it should be improved.
Most importantly do not embarrass yourself with the demand for samples refund if it is not the product you were yearning for, that is why it is called a sample.
You can request the supplier if he is willing to deduct the sample cost from the order amount, in case you will do the mass production with him/her.
Are you producing a product that requires a mold?
Before you order a sample, we advise you to ask the manufacturer for a 3D sample (that you will pay for, of course).
Want to make a product and then changes in the graphics / colors / size and so on, but producing a sample costs a lot? Or you are not sure exactly if the factory understands the result, you are looking for?
Always do product simulation. This will ensure the prevention of misunderstandings between you and your manufacturer.
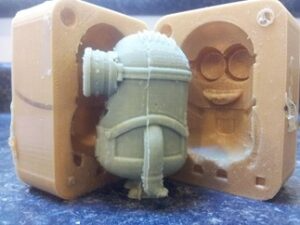
How to inspect your product’s samples?
There is a tendency to think that a sample must be perfect.
The truth is that this is exactly why you buy samples.
The reason for ordering samples is to examine all the requirements, quality of the materials, colours, prints, etc., but the sample is not the finished product.
You have received a sample that you do not like 100%. Make sure to work with your supplier, make sure he/she will understand and learn how to improve the next sample to your satisfaction.
When you order a sample for $ 10 do not expect to get your dream product, the one that you have been fantasizing about for years. Samples are for getting a first impression on the product and that does not mean that this is the final product you will manufacture.
Samples help us understand what the factory offers and what the quality level of the product is. Then we draw our conclusions and find out with the factory whether we can accept and design the product according to our requirements or not.
Keep in mind that in most cases the factory sends you a sample from a stock that they already have. A stock product may look neglected because it has been sitting in warehouses for a long time, maybe it has accumulated a bit of rust, maybe it has been used in the past as an internal sample, etc. (This is different from a situation when the factory created a sample for you from scratch).
Therefore, do not expect the first sample to be the perfect product.
I received the product’s samples, what’s next?
Samples are for testing the ability of the factory and whether the product is right for you. All the cosmetics of the product are less relevant.
I come across clients who think the sample they receive is the end of the story. They see the samples and because the packaging is a bit wrinkled or does not look good with the colors of their logo, they doom the sample to failure.
My friends, if the sample is the complete finished and perfect product, then why order it?
If you see a piece of plastic you don’t like, take care of it at the production stage.
If a sample arrived scratched it could be from the shipping process or because it is from stock.
Either way, you can learn from this sample and that is exactly the purpose for which we ordered it. For example, now we now that it is necessary to think of a suitable packaging that will prevent scratches when sending the product to the customer, we can discuss with the supplier and aggree that in mass production a scratch at the depth of X and length of Y will be considered invalid and will not pass inspection.
Remember! Samples that are sent from factory’s stock are not always 100% perfect according to your imagination.
It is very important to remember that we are responsible for the final product. If the samples suitable for me at 80% it is excellent, the rest of the 20% we can handle.
Here are few examples of things that can be easily fixed
- Packaging
- Types of batteries
- Scratches of all kinds (it is mandatory to speak to the factory or the agent and monitor it during production)
- Colors
- Logo
- Bad smells
All the above can be fixed and there is no need to rush and terminate an option for future business with the supplier due to “defects” that are repairable.
Bottom line, it’s important to check the quality of the product itself!
- Test the product in the conditions and everyday situations that your customers will use it.
- Try to simulate prolonged use of the product and check its durability and abrasion resistance.
- Check if the product provides solution to customers’ needs and pain points. Do you provide better quality or extra functionality that your competitors don’t?
- Give your samples to different people, friends, family, and neighbors, ask them to use the product, and give their opinion.
- Finally, after you have performed the necessary tests (it is recommended to prepare a checklist in advance so you can mark and document your tests), you can perform tests in extreme situations.
Over Time Quality Inspection
Sometimes we check samples, and the quality is good but then after a while, problems are revealed in front of the customers, so how can we try and make sure our product’s quality over time?
So of course, that we highly recommend not to give up on a sample it is obvious, but we know that not everyone has tools like our company for testing the quality of factories and products over time so what exactly you guys can do?!
- Check what quality control the factory uses (if at all). A factory that produces an electrical product for example, and doesn’t have a basic ISO, our recommendation is to stay away from this factory. Check what quality certificates the product has and check those certificates validation, because there are many suppliers who lie, and it also says a lot about the supplier.
- What kind of QC the factory does? It is very important! You need to see the quality system and not settle for one or two people that are checking the line.
- If the product has been already sold, asks to see the reviews of the product.
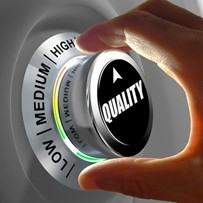
How can we minimize risks when we manufacture a product in China?
- Even when you do not make a product from scratch, but really want to see the final product including packaging, logo, etc.; because you can’t wait or the sample costs are high or you want to make changes (graphs/color/size, etc.) or you don’t want to spend more money on a final sample and wait for production time, you can always do a three-dimensional simulation.
The cost of the image of 3D imaging will cost you half of the product shipped to you, and of course if you do it in China and submit it to your supplier, he will have to compare it with your original product after production.
Of course if you need 3D simulations in China you are welcome to contact us
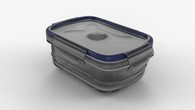
- Verify expectations – after confirming the sample, ask for another sample from the production line, before approving the goods for delivery. This will save a lot of problems between you and the supplier.
- Do you test remotely a product in which color is important, by receiving pictures?
Keep in mind that each color looks different in the image due to the shooting angles, light, print quality, and the material on which it is printed.
- Color should be agreed on only after a sample, and only by a clear indication of the PANTON type. Otherwise, you will always have differences in the result.
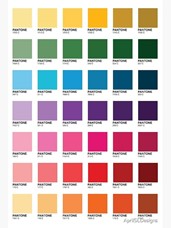
To sum up,
I want to share with you a story that my father always told me when I was a child.
A story about a poor family with a child that found a chicken egg.
The boy imagined how he will raise the chicken and sells it in the market. How he will make money, will buy a wagon, will use it for doing deliveries. From the money that he will earn, he will build his parents a beautiful house, when the neighbor’s daughter sees all of that, she will want to marry him, they will move to the big city and raise their children there…… meanwhile the egg fell off the table and broke.
Before building the whole future of your product on a good or bad sample, keep in mind that the meaning of samples is testing!
This is one step. Do not take the glitches of the samples as the end of the process, this is only the beginning of performing a correct and smart process.
Samples are part of the process and whether their cost is $ 10 or $ 300 it is not always relevant when we build a business, and in most cases, we get the cost of the samples back, so don’t skip on their purchase.
Before terminating or building a rosy future based on samples, please understand that this is a very necessary step but is only a first step, from here you will start evolving further.
Always remember! To manufacture a product is a process, it is not one step, and we are done. Patience and persistence, and of course hard work with the right people will always lead you to success.
Looking to improve your production costs? The quality of your product? Want to expand and are interested in manufacturing a new product?
As always, feel free to contact us at +972-8-86202525 or leave us details here and one of our customer success managers will get back to you for a free consultation regarding our sourcing, product R&D, and manufacturing services.
*THE CONTENT OF THIS ARTICLE IS A COLLECTION OF DAILY TIPS FROM THE LEADING FACEBOOK GROUP
#Everyday Tip for E-Commerce – Amazon Alibaba eBay and everything in between