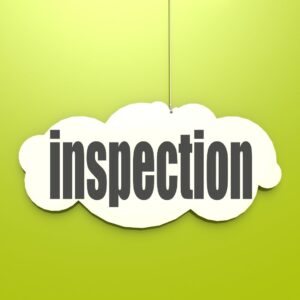
Amazon FBA Product Inspection and Quality Control for Ecommerce in China
Everything you need to know about Products Inspection
One of the crucial stages in the production chain is the inventory inspection prior leaving the supplier’s facilities.
Performing a quality check by a third-party inspector for your products is one of the essential parameters that will help to prevent losses and determine whether your product will succeed on Amazon or not.
This ensures your product meets your design and quality expectations. One batch of poor-quality products can ruin your products and brand.
Delivering consistent high quality is the key to positive reviews and customer experience.
As e-commerce traders and entrepreneurs, I’m sure you already know all that and understand the importance of product inspection, but did you know?
- What are the different types of inspection?
- Which type of inspection is better?
- Factory Audit
- Can I trust Alibaba Trade Assurance?
- What is AQL?
- What to do if the inspection failed?
- The inspection went well, but when I received the shipment I discovered problems with the product
- How to choose a quality and reliable inspection company?
- What is being checked during an inspection, and how much it cost?
- DROP TEST
There are 3 main types of inspection
Most Amazon sellers know and often choose to have inspection in China, before sending their inventory to its destination. This type of inspection is better known as Pre-Shipment (which has different levels).
The thing is that not every product needs a Pre-Shipment test. For some products an inspection before packing or while manufacturing is better (a QC which usually eliminates the final inspection (in some cases).
When will we know if it’s better to inspect the products before their packed and ready for shipment?
- When the product is delicate and if we open its package, we might ruin the product.
- When it is not possible to detect the fault at the final state of the product, and it can only be visible and identified at the preliminary stages.
- When we need to make sure that certain steps in the production line were not skipped.
- When the complete product is manufactured by using several factories
- When there are failures that we are aware of, but at the last stage of production we will not be able to check them.
99% of the factories approve inspection during production.
If a factory does not allow you this type of quality check, I advise you not to work with it. Factories/suppliers who are not willing to undergo an internal inspection probably have something to hide.
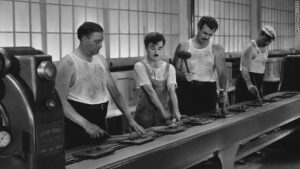
Another quality test (QC) that exists and not many are familiar with, is an audit of the plant itself.
Why is Factory Audit important, and is it necessary?
I would like to answer this question with a story.
Our company provides services for ecommerce traders and professional consulting services to international e-commerce service providers.
About a year ago, I consulted for an inspection company, and joined an inspection they conducted for one of their customers.
After long walking and searching, we finally found the “factory” (feel free to see the picture of the “factory” below).
$ 22,000 order, and we found was no trace of the merchandise. The customer was broken and tried to locate the supplier.
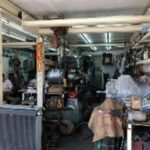
Another case I would like to share with you happened to our new customer, who asked us to inspect her products before shipping them from China to the US.
The customer is lovely, she was all excited for her Amazon adventure, and she kept complimenting her supplier.
The first inspection failed according to the customer’s standards.
After two weeks (the goods were supposedly repaired), we had a second inspection and it failed again.
The supplier starts to be less nice than before. Moreover, it turns out that the supplier is not the factory, the supplier no longer behaves so nicely and after repeated promises given to the customer, we made a third inspection.
Again … failed!
The customer went through an exhausting process of unending frustration, refunding payment through Trade Assurance, wasted months, lots of money, and was left without a product.
That is why it is so important to do a full inspection or audit your factory/supplier / manufacturer in advance.
You can at least have a technological inspection, receive a professional opinion, and not just compromise with a partial inspection before shipment.
Even if you pay a little more (by the way a technological inspection is even cheaper), this expense will save you long processes, disagreements, disappointment, and a lot of money down the road.
Remember! On the Internet, everything can look big and impressive, you need to work with people that you can trust.
Product inspection is important for your peace of mind and security.
In addition, when you audit your supplier, he will do his best, because he knows you are watching him. This is a necessary step, and it is advisable not to skip it or save on it.
Wait … Doesn’t Trade Assurance protect me in case of the quality control has failed?
Alibaba’s Trade Assurance is a transaction protection service to enhance the trust between buyers and suppliers, with Alibaba acting as the intermediate assurance party.
Therefore, in case of a dispute, Trade Assurance protects you and protects your supplier as well.
Trade Assurance does protect you if you have stones and instead of products inside your cartons or units are missing.
However, when you are not satisfied with the results of your product’s inspection, your supplier knows that most chances are that he has nothing to worry about and that he will receive his money from Alibaba.
How come you ask?
Trade Assurance disputes can only be field if the quality control clearly shows that your factory/ supplier has failed to match your defined quality requirements.
However, your supplier has already received the payment (part of it or all, depending on your agreement and if you preformed the inspection before shipping or after receiving your products).
Moreover, to determine that the quality check did in fact failed, you must issue another inspection, using a company that is approved by Alibaba.
Those companies claim an inspection failed only if it doesn’t meet the AQL (Acceptance Quality Limit) standard.
The AQL standard is used by the best and leading inspection companies for acceptable quality level.
What is AQL?
AQL standard is defined as “quality level that is the worst tolerable”. It is a well proven and widely adopted international standard ISO 2859.
Its definitions result from statistical analysis and probabilities for forecasting quality problems based on BATCH TEST results.
There are different test levels.
The higher the level, the lower the probability of problems. With each increase in the test’s level, so does the cost of the test increased (because a higher percentage of product’s units from the production are tested).
Our company is also using the ISO 2859 standard, and as I mentioned, it is a standard that we can define by levels of testing.
For example, you can negotiate with your supplier in advance that the production fault won’t exceed 2%.
ISO 2859 will not always meet your personal standards; therefore, you need to learn and understand it.
Remember! when talking about selling on Amazon, your quality check standard should be strict, because Amazon’s clients are less forgiving.
Therefore, it is always advisable to work with an inspection company that works in accordance with the international ISO 2859 standard and to define in advance the quality and level of accuracy of the product in detail, in order to minimize your risks.
So, what can be done if the inspection has failed? How do you solve a dispute with your supplier?
The most important thing is to calm down.
No one did anything intentionally so one has to understand that getting too angry will tear the rope.
You must solve the current problem and at the same time, find a solution for next orders (in case there will be another problem).
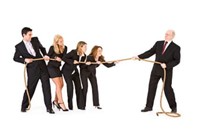
The supplier should be asked to repair the faults, if possible, at his own expense.
Of course, there are issues that he will demand payment for, and at this point you will start the negotiating about future orders.
Make your supplier realize that you have more opportunities in line and in doing so he will minimize the loss incurred.
Don’t get stuck, find a temporary solution. Meaning, take the products that are usable and work with those, then start to figure out how to handle with the defective units.
Honest and open communication about the damage and your personal situation is very important.
Do not threaten the supplier in any way, just explain the heavy damage it will cause you, in the hope that it will indeed help you resolve the matter in a peaceful and respectful manner.
Offer creative ideas of your own to solve this situation and be prepared to part a few bucks.
If all this still does not help or you are afraid, don’t know how to proceed from here?
You are welcome to contact our company and we will try to help you by using a little more force on our part, although this is also not a guarantee sure success, but it is another option that you should consider.
What can be done in case I ordered goods from Alibaba, the inspection passed, but when the goods arrived at their destination it turns out that it is damaged or part of it isn’t what I have ordered?
First, if the deal was not executed under Trade Assurance, there isn’t much you can do.
If the transaction was made under Trade Assurance, you can apply for a refund, but since it is a long process and you have already received the supply, you are a bit in trouble and there is only a 25% chance of you getting a refund.
You can complain to Alibaba about anything, the question is if someone will listen to you.
Unfortunately, 90% of these complaints are not dealt with.
Usually, the supplier is warned or in rare cases is banned from selling on the platform.
In case the supplier admits to his mistake, he can be sued. It costs quite a bit, but you will probably win.
The best move is to avoid such a situation in advance by inspecting with a professional, reliable, and independent company.
Note that Alibaba’s business model is based on monthly subscriptions.
Their interest is that as many vendors as possible will join the platform. Their first concern is that a supplier will join their platform, and only afterward his credibility.
Thus, all diamonds, flags, and logos that you check on Alibaba when you are searching for a supplier are not 100% accurate.
So how to choose a quality and reliable inspection company?
Here are some rules of thumb that will help you make the right choice
- Make sure that the inspection company complies with the ISO 2859 standard.
- If you already know a reliable company, use its’ services, even if it means you will have to pay a little bit more – it’s worth it.
- Always work with an impartial company.
Sometimes we work we the same factory for a few times already, constantly performing inspections and everything comes out fine, each time. However, we receive negative reviews repeatedly or maybe our products arrive to the warehouse and some of them are not at the quality level we expected.
This could happen when the inspector is not doing his job properly, because most likely he is affected by a close relationship with the supplier or worse, the inspector receives “bonuses” from the factory.
How can you identify such a scenario in advance?
Avoid using a company that your supplier recommends (there is a conflict of interest here that implies cooperation).
Another thing to do is to rotate between different inspection companies and thus avoid this problem - If you need an inspection in China, it is advisable to choose a company that has branches in important places like Shenzhen, Guangzhou, Ningbo etc.
Note that most companies can’t cover the whole of China, so they use sub-companies that usually don’t do a great job. - Work with an inspection company that is recommended by Alibaba. Go to this link to alibaba.com and find all the service providers (including our company) that Alibaba certifies and trust.
- Inspection is done with a clear and professional report!
Not by video or unnecessary lives that will keep you awake early in the morning, give you a false impression and a false sense of security. - Work with a reliable, professional company that cares about you and your success.
For example, a customer called us with the request for urgent inspection from the next day, and urgent shipping as well.
None of our inspectors were available at such short notice, so I asked Jimmy, our retired employee, for help. He immediately answered to the call, left his family, and went to inspect the client’s merchandise.
Work with a company that is experienced, located in the same country where your factory is, with the right certification, professional, and large enough to give you solutions in various situations, especially when the unexpected pop up.
What is being checked during an inspection, and how much it cost?
The price of an inspection depends on the inspector working time, cost of travel, the complexity of the examination, how many inspectors are needed, level and expertise of the inspector, is there a need for lab testing, etc.
First and foremost, it is important to understand what you want to check.
As mentioned before, there are different types and levels of inspection and inspectors.
For example, if it is a basic level inspector, then the cost is according to the inspector’s daily labour hours.
In general, standard inspection checks that all the units are packed and there are no stones in the carton.
A sample test of about 10% of the production is performed, unless another request has been made in advance by the client.
The inspector tests the product itself and not the ancillary products. If there is a “bonus” in the package, the inspector won’t test it, he will just make sure that it is there. So, if the product has reached Amazon and the “bonus” is defective or after a month the product is not working well, this is not the type of inspection you should have.
It is important to make clear requirements for performing the quality check and remember of course that prices vary per request.
By the way … if you do the production process with us, then we will perform a basic inspection for you, because at the end of the day it is our name 😊
Another important test is the DROP TEST
90% of the factories do not approve to do this test.
The importance of the test is to check the durability of the packaging that the supplier has performed, to make sure that the carton will withstand the pressures during the logistics chain until it reaches its destination.
Each carton probably has a breaking point and if your supplier does not pack your products properly according to the weight and volume, light/medium blows can sabotage your whole shipment.
It is highly recommended to perform the DROP TEST.
If you supplier does not approve this test, ask him for the reason.
The reason is usually that he fears that there will be damage to the products (while they are still in his factory).
What if the product is fragile, is it still recommended to perform the DROP TEST?
In this case, we need to check the DROP TEST TABLE.
This table checks the maximum pressure that should be applied to each carton, according to its weight. To check the right pressure for the test, using the DROP TEST TABLE, we need to know a lot of details that are not always available to us.
For example, the thickness of the carton, the breaking point of the inner carton, etc.
The mathematical formula depends on so many variables that even if the product is fragile, we recommend checking at least one carton.
It is very important to perform a drop test on your products before shipment. This way you can make sure that your inventory arrives safely at your warehouse/Amazon Fulfillment Centers.
Ask your factory or the inspection office to perform the test for you.
By the way, we have a unique equipment on our warehouses to perform the DROP TEST.
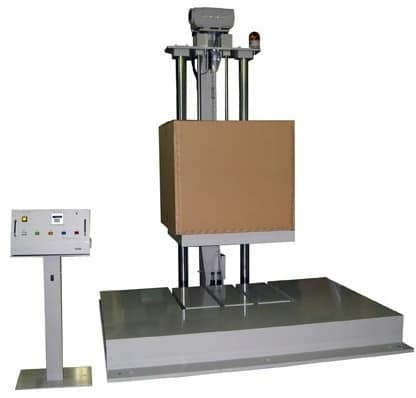
Special equipment for
DROP TEST
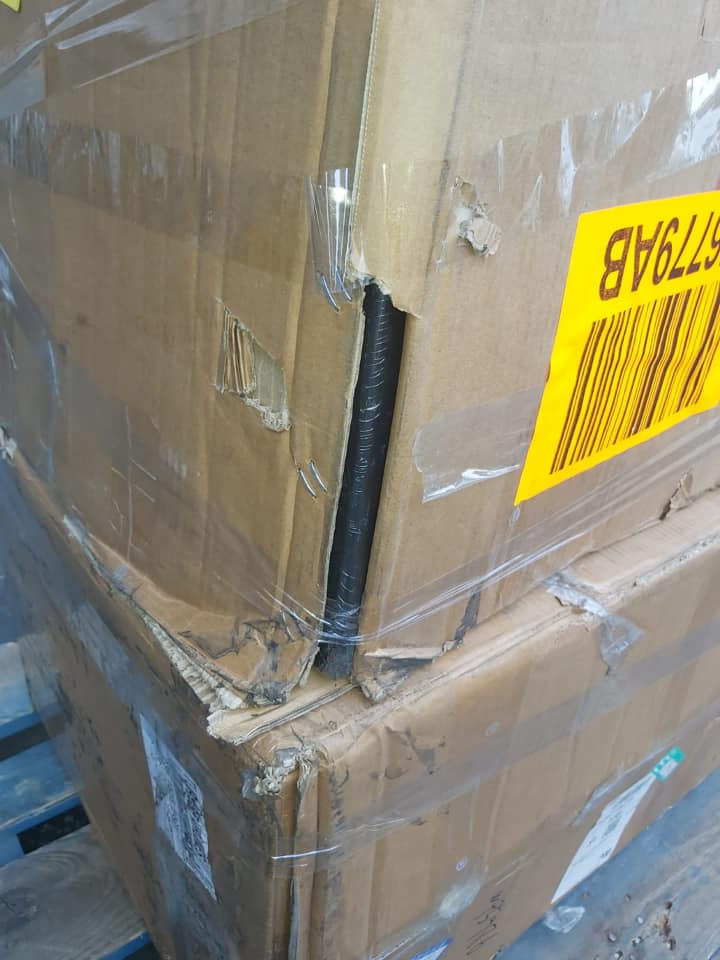
Wrong packaging
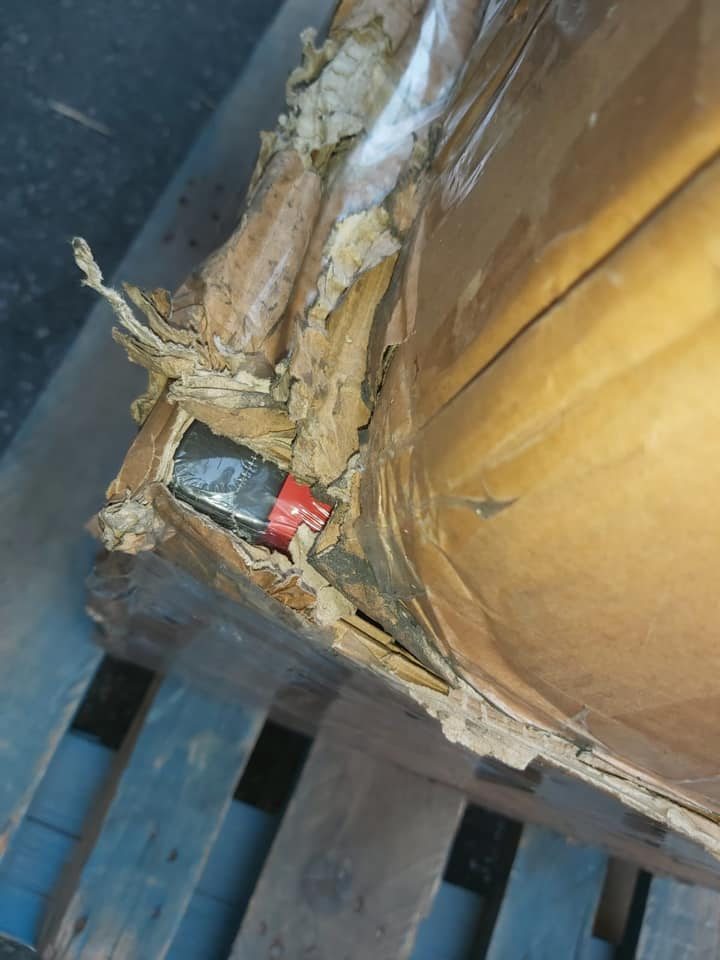
Carton was damaged
during transportation
In conclusion…
Never give up on inspection just in order to make it to a shipment or from fearing that shipping costs might rise up.
Do not go to a foreign unknown company just for $ 20-30 less.
Always perform an inspection, even if it’s a factory you’ve worked with 1000 times before!
Finally, there is no reason to work with a factory that refuses to go under inspection, because for sure it has something to hide.
Have more questions, interested in free consultation, want us to quote your next inspection? You are always welcome to give us a call 086202525 or leave us your details here FBA Amazon Sellers, and we will get back to you as soon as we can.
I wish you a successful inspection free of faults 😊
- 2021 GameOn Group C.L LTD All Rights Reserved
*The content of this article is a collection of daily tips from the leading Facebook group
#Everyday Tip for E-Commerce – Amazon Alibaba eBay and everything in between